Wavy cuttlefish
-
- Marina, Hajar, Théo, Robin
Origines du projet
Pensant aux jouets pour chats, nous connaissions pour certains les poissons robotiques nageant dans l’eau. Et en partant de ça et cherchant des projets intégrant la soft robotic, nous sommes tombés sur le Bionic FinWave de l’entreprise Festo. Convaincu par ce poisson, nous nous sommes inspiré de celui-ci pour créer le notre, notamment créer ce système ondulatoire des nageoires latérales.
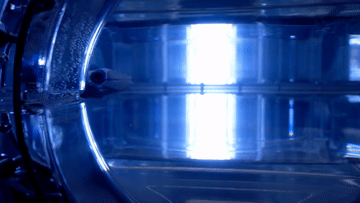
Inspiration, pistes et ressources
Cuttlefish Inspired BionicFinWave Underwater Robot Uses Fins to Proper Itself – Tuvie Design
ref artistique Theo Jansen
Déroulé
Le principe important de ce projet est le l’ondulation créé par un mouvement haut/bas de plusieurs petites bielle/pattes.
1. Prototypes
Nous avons tout d’abord réalisé un prototype avec du bois et des pailles afin de comprendre le mécanisme. Cela ressemble à un vilebrequin, l’arbre au milieu tournant, faisant bouger la tige permettant un mouvement haut/bas. La tige étant glissée dans une paille, elle coulisse dedans, ainsi il y a toujours la même longueur dépassant (celle de la paille).
2. Modélisation du système
Il a ensuite été fait une modélisation 3D d’une partie du système, qui va être dupliquer puis mis bout à bout avec un décalage d’un quart de tour pour obtenir la propagation d’une onde le long du système.
Nous allons ensuite modéliser et imprimer grâce à l’imprimante 3D disponible au FABLAB de l’IMT.
3. Moteur
En parallèle nous avons commencé la programmation et les tests de moteurs. Nous sommes tout d’abord parti sur un servo-moteur, seulement il ne peut faire en continu des tours complets. Nous sommes donc passé ensuite sur un moteur à courant continu.
Lien du circuit électronique : https://app.cirkitdesigner.com/project/a792a1b7-b534-4ce2-ba44-ae935a4ac74d
4. Membrane
Pour la membrane nous avons décidé de tester de la faire en silicone à prise rapide (ECOFLEX). Nous en avons fait 2 : une purement en silicone et une deuxième avec du tissu au milieu.
⚠️ 🤦 Nous n’avons vu qu’après avoir fait notre silicone qu’il y avait une balance et que les mesures entre le produit A et B devrait être exactement identiques. La première version silicone (sans tissu) a l’air d’avoir fini pas prendre, au bout d’1h30-2h mais celle en tissu peine davantage.
Nous avons pris des couvercle de boîtes qui étaient à disposition dans la salle, ayant les dimensions que l’on souhaitait. Notre membrane en silicone mesurent environ 9.5cm de long et 7cm de large.
Nous avons également fait une plus grande plaque, pour faire d’autres tests si nous avons besoin de plus grand.
5. Système
Nous rectifions quelques données pour l’impression 3D, nous pouvons être plus précis sur nos mesures.
Nous avons lancé l’impression un soir avant de partir au FABLAB, afin que nous perdions le moins de temps possible avec l’impression, l’imprimante 3D ayant travaillé la nuit pendant environ 9h.
En montant les pièces, nous nous sommes aperçu que la pièce fixée au moteur frottait contre le support. Ainsi nous avons poncé/coupé (papier à poncer, rappe, scalpel chauffé, …) le bord du support pour que la pièce puisse passer et ne frotte pas à chaque passage.
Il s’avère également que les pâles sont un peu trop grandes, impliquant que le support lui permettant de coulisser ne tombe pas en face des trous pour qu’il se fixe.
6. Fixation de la membrane
En même temps, nous avons découpé les membranes en silicone que nous avions faite, afin qu’elle soit moins large sinon elles retombent dû à leur poids (nous les avions fait avec des mesures assez larges pour avoir des marges et recouper comme nous le souhaitions).
Nous avons également fait des membranes avec des pics en bois, afin de rigidifier la structure.
7. Premiers tests
Nous avons pu effectuer les premiers tests de fonctionnement avoir le moteur après avoir arrangé la pièce.
https://lowsoro.com/wp-content/uploads/2025/02/VID202501291117122.mp4
8. Nouvelles pièces
Afin de régler les soucis de taille et de modification de pièce, nous avons pu en refaire (grâce à l’imprimante 3D personnelle de Robin), afin également d’agrandir notre système et tester un meilleur mouvement d’ondulation.
9. Nouvelle membrane
Au vu de la taille qu’allait faire notre système, le vilebrequin, nous avons décidé de refaire des membranes, même si nous n’avons pas encore pu tester les précédentes. Nous avons prévu 2 avec avec des batônnets (éviter le gâchis de la quantité de silicone produit) et une seconde sans batônnets (en coupant en 2 partie la grande bande). Nous avons pris du carton et du scotch afin de compartimenter, n’ayant pas besoin de bandes très larges.
10. Assemblage et personnalisation
En parallèle le nouveau système, avec les pièces fraichement imprimée dans la nuit, est assemblé. Nous l’avons également collé la structure à notre support (un calendrier).
Après les premiers tests en fonctionnement, le vilebrequin devait être maintenu en bout mais celui bougeait, avait un mouvement de rotation sur la dernière pièce, nous pensions que mettre un des triangles de support allait bloquer le système. Ainsi nous avons penser à faire un support différent : une pyramide en bois, avec un bâton horizontal sur lequel la dernière pièce du vilebrequin pourrait s’appuyer dans sa position basse, sans être bloqué.
Le projet étant à la base un poisson, nous avons alors customisé la pyramide en bois, avec du tissu avec de lui faire prendre vie.
11. Etapes finales
Nous avons ajouté la membrane au système : seulement tout se bloquait et peu de mouvement était effectué, nous avons modifié cette dernière